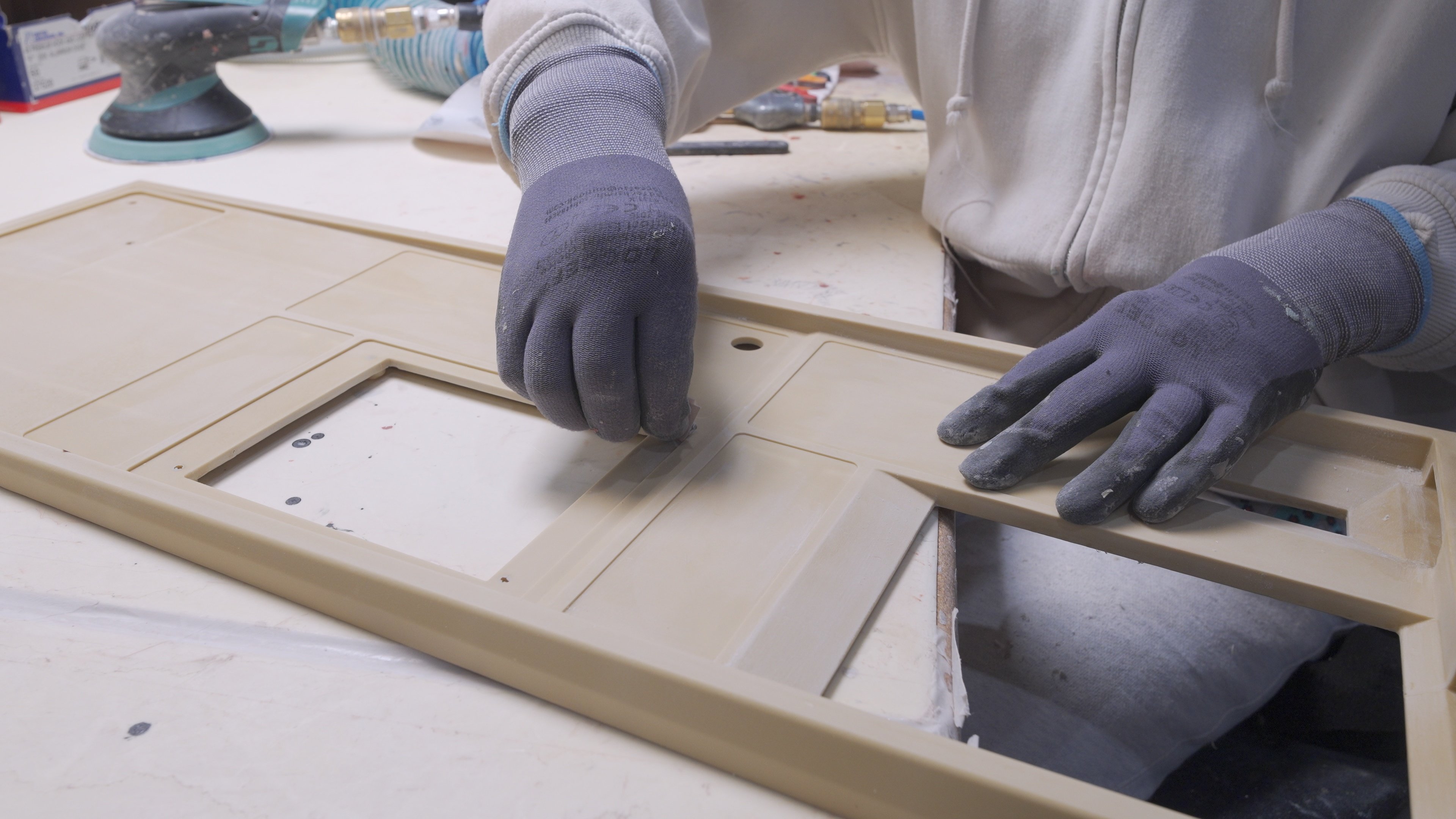
Process Comparison
Below are considerations that must be evaluated when making a molding technology decision for production. There are many factors (design intent, cost, functionality, quality) that need to be balanced when determining the most economic and qualitative method to mold your plastic application.
Your final technology choice will be based on annual volume of parts to be made, part size, tooling investment available, the parts physical properties, design factors needed and available lead times. Contact Thieme Corporation to assist in understanding the advantages, benefits and economics of making the RIM molding choice for your next product application. Thieme will guide you through evaluating RIM for the entire process from part concept to final assembly logistics on your plant floor for your next plastic application.
RIM
Injection
Thermo / Pressure
FRP
Structural
Sheet
RIM
Injection
Thermo / Pressure
FRP
Structural
Sheet