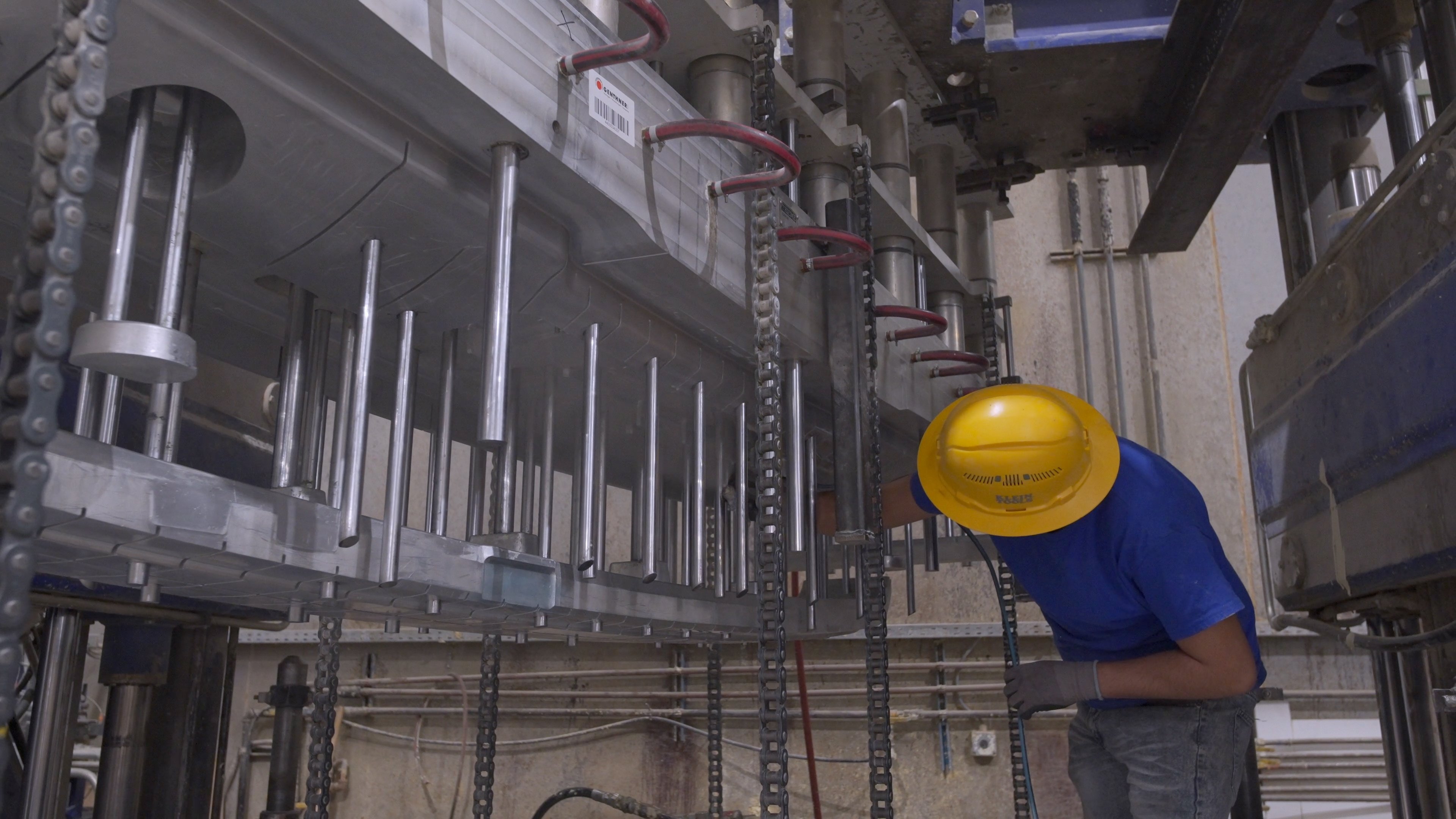
Use of RIM Molding in Medical Technology
When buying new medical devices and equipment, buyers in private practices and hospitals are increasingly placing value on appealing and ergonomic design aesthetics. In the case of equal functionality, the design and the functional aesthetics can be crucial to the market success of a new medical device.
RIM Molding and Polyurethanes – Medical Enclosures
The polyurethane material (PUR) offers diverse options for medical device designers. PUR not only offers the designer extensive design, molded-in functionality and construction flexibility but also exhibits particularly favorable material properties which are significant for medical applications. Examples of this include but are not limited to, low weight, insulative properties, EMI shielding capability, large part manufacturing, variable wall sections, chemical resistance, and easy cleaning.
A favorable cost structure of the PUR and RIM Molding process is also a factor here especially when volumes of 5,000 part per year are concerned. It is a very economical process when low unit quantities in medical technology field are required, from a few hundred units to thousands of units annually.
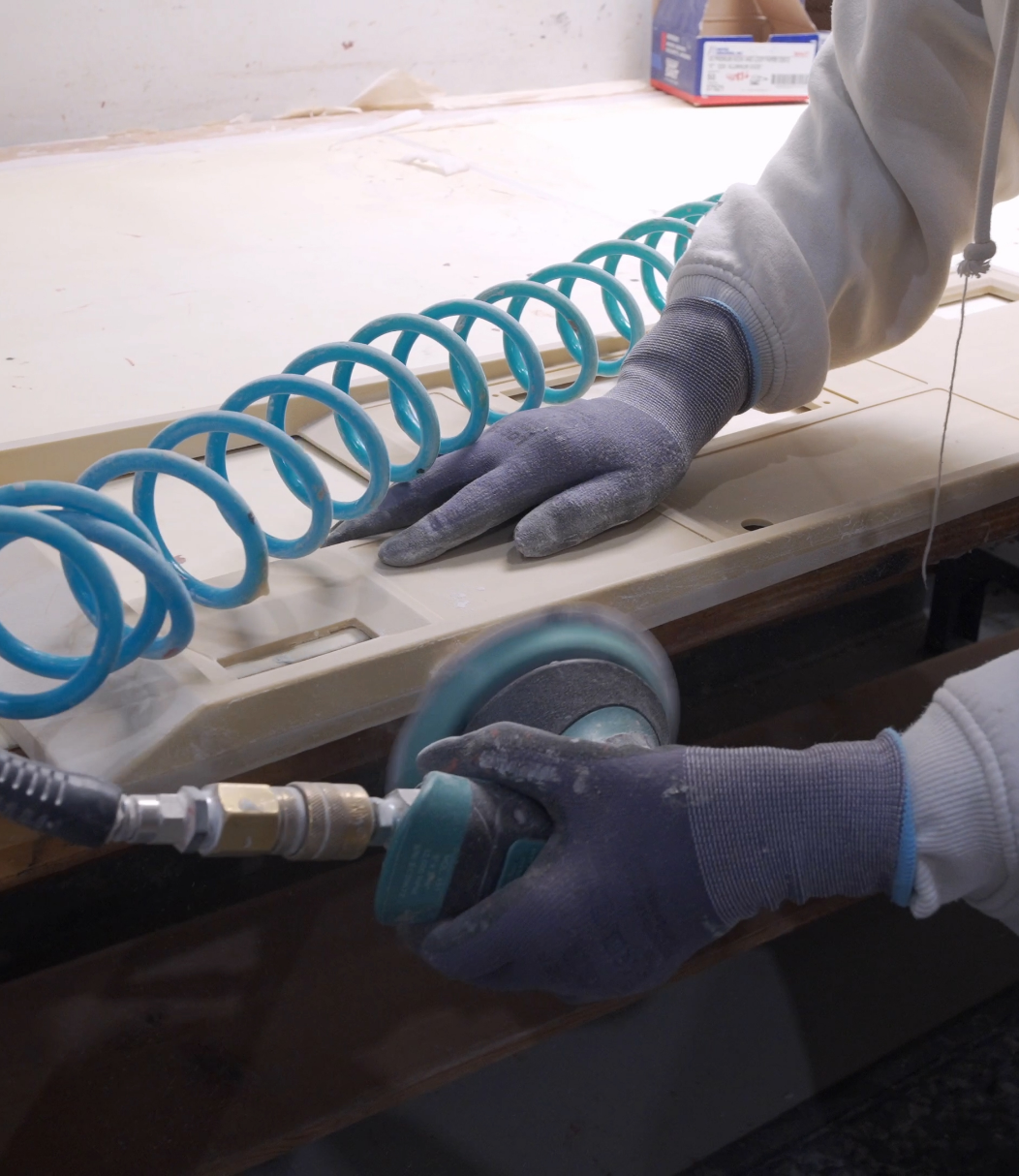
Examples of recent medical applications include:
- Analysis Device Housings
- CT (Computer Tomography) covers
- Dialysis machine structures
- Mammography machine covers
- Water Treatment carts
- PET Covers
- Dental Light, chair and cleaning machine covers
- Medical Trays
- And many more
Advantages of RIM Molding for Medical Enclosures
Polyurethane, the material for most medical and scientific device applications. Virtually no other material combines aesthetics, ergonomics and function into such an ideal form.
Advantages of the Polyurethane Material systems:
- Economic efficiency
- Design Flexibility
- High dimensional stability
- High rigidity
- Low part weights
- Impact resistance
- Sound insulation
- Great thermal properties
- Chemical resistance
- UL 94 VO compliant
Advantages of PUR and the RIM Process:
- Use of cost-effective aluminum tooling
- High degree of design flexibility
- Minimization of assembly cost due to molded in features, functional integration
- Complex three-dimensional geometries
- Ability to mold large, deep draw parts
- Ability to make cylindrical parts
- Creation of fine details in the design such as holes, slots, wire guides, etc.
- Comprehensive surface finish and paint options
- EMI shielding is possible
- High degree of design flexibility
- Fulfillment of physical characteristic requirements
- Reduction of logistics costs
- Reproducibility
- High reproduction accuracy