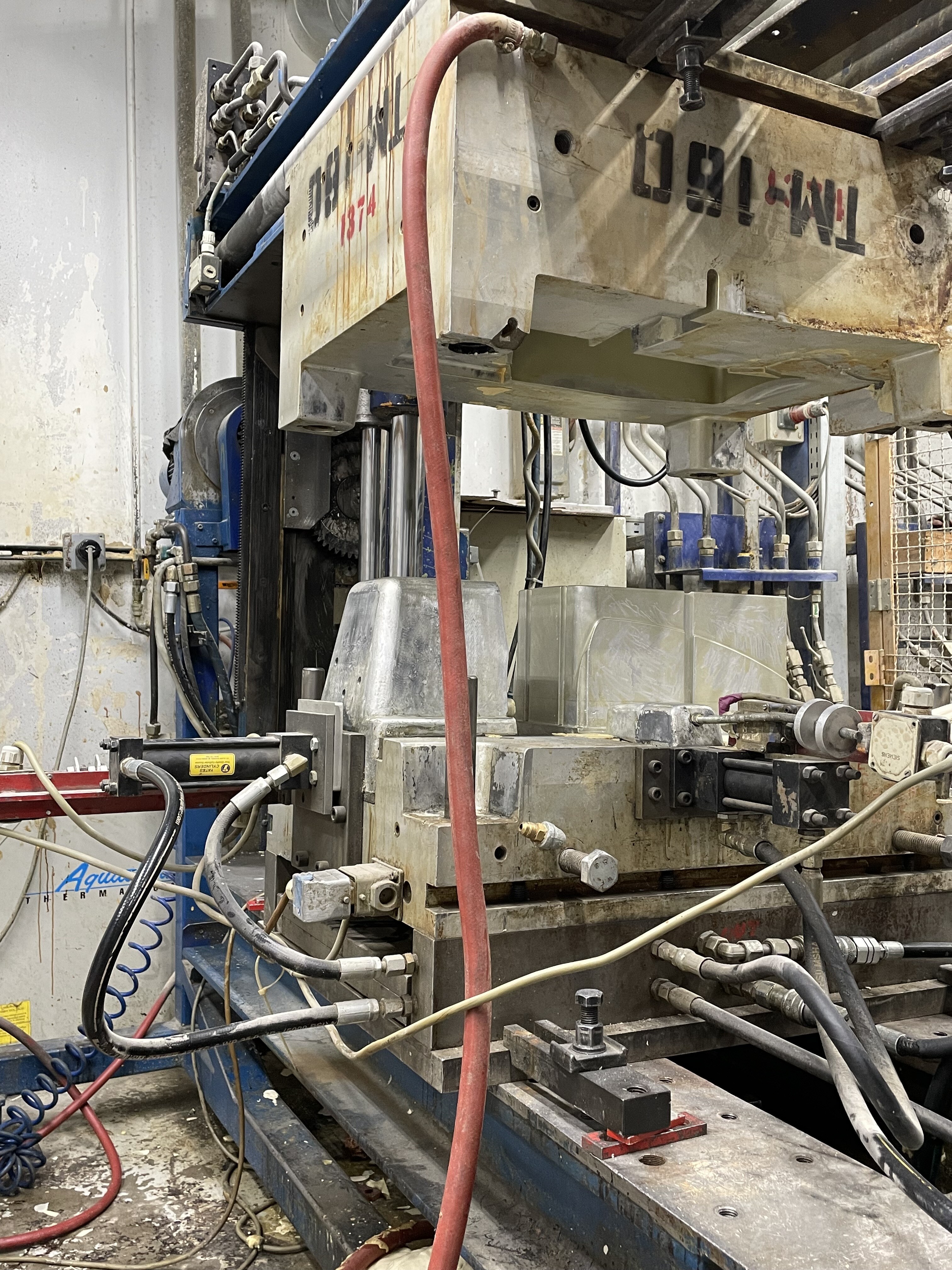
The Reaction Injection Molding (RIM Molding) Process
The RIM Molding process begins with two liquid reactants, a polyol component (B) and an isocyante (A). These are contained in separate temperature controlled day (feed) tanks equipped with agitators. When a shot is called for at the mix head at injection, from these tanks, the polyol and isocyanate are fed through individual supply lines to metering units that precisely meter both the A and the B components and supply them to the high pressure mixhead.
When injection begins and valves in the mixhead open, the liquids are impinged upon each other at pressures between 1,500 and 3000 psi beginning the high velocity mixing of the two components. From the mix chamber, the liquid flows into the mold at approximately atmospheric pressure and undergoes an exothermic chemical reaction, starting the foaming process inside the mold cavity and subsequently forming the polyurethane polymer part inside the mold. Shot and cycle times vary, depending on the part size (up to 100 pounds in a single shot) and the type polyurethane system used (rigid, foamed, elastomeric, etc.).
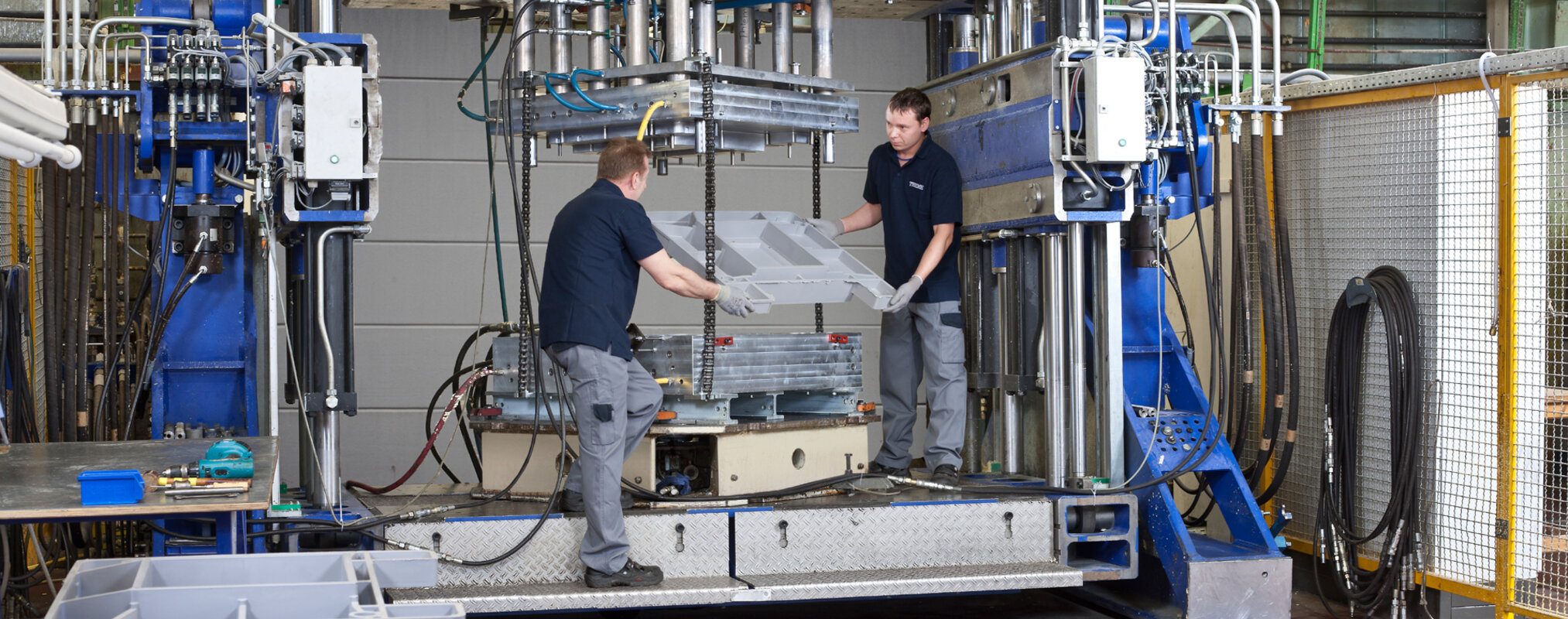
How Long Does the Reaction Injection Molding Process Take?
The duration for completing the RIM process can vary based on several factors, including the complexity of the part being molded, the size of the production run, and the specific requirements of the project.
Generally, RIM is known for being a relatively quick manufacturing process compared to certain alternatives, but the exact time can range from a few minutes to several hours per part.
It’s essential to consider factors such as mold curing times, part cooling times, and any additional post-processing steps that may be required for finishing. The efficiency of the RIM process, along with its ability to produce large, intricate parts, contributes to its appeal in various industries.
Advantages of Polyurethane Reaction Injection Molding Process
Unlike other molding methods, RIM offers unmatched advantages in design flexibility, cost-efficiency, and accommodating unique part sizes. While reaction injection molding may entail a slightly longer production time, its benefits in design, flexibility, and overall cost-effectiveness far outweigh this drawback.
The reaction injection molding process outshines injection molding, vacuum-forming, pressure-forming, and cast molding, making it a superior choice for various applications. RIM excels in accommodating various part sizes and unique designs, providing precision and control over velocity. Its superior performance resonates positively with both customers and end-users, highlighting its effectiveness in the plastic manufacturing domain.
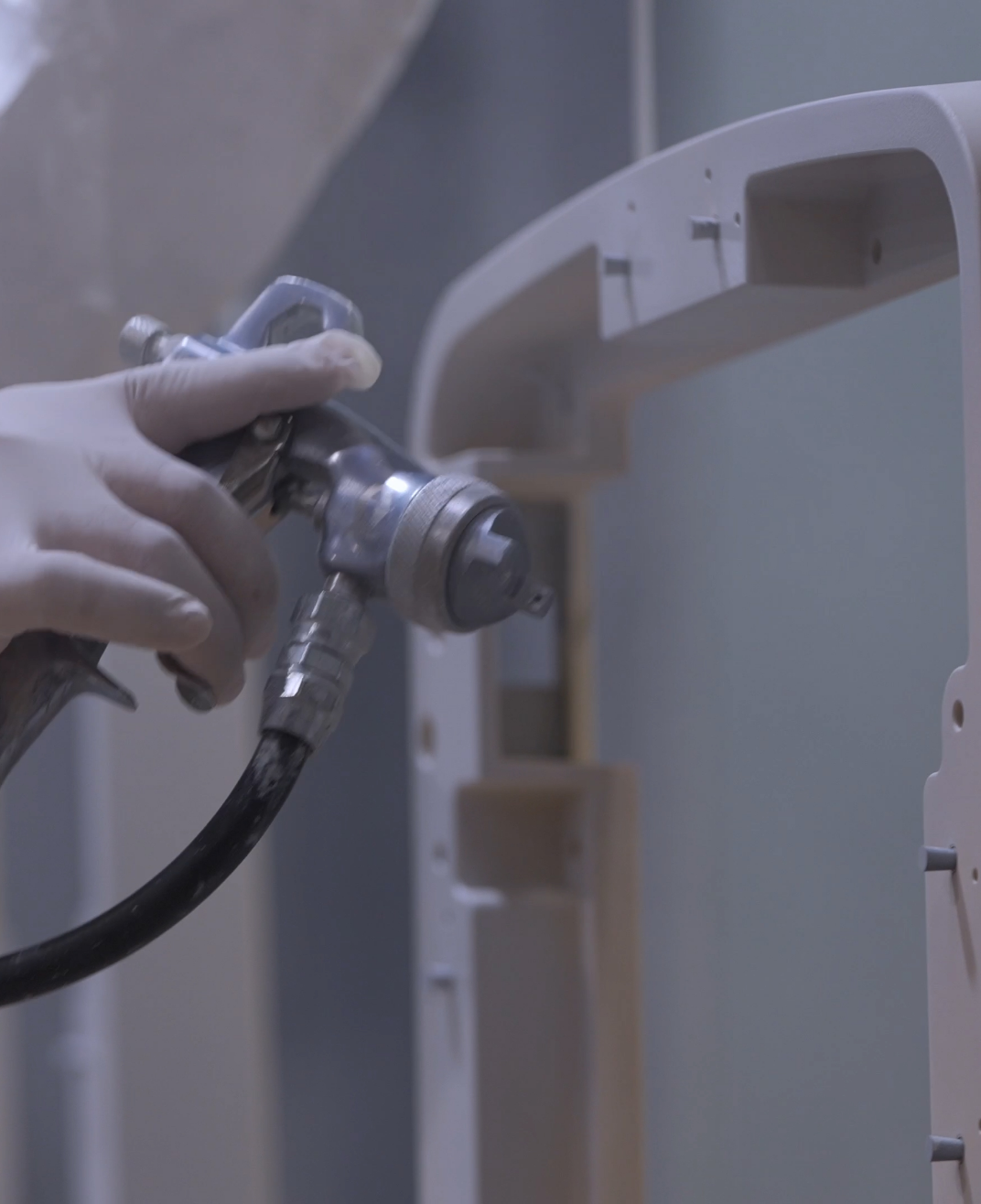
Contact the Reaction Injection Molding Process Experts at Thieme
Thieme offers custom reaction injection molding solutions for a wide variety of devices and industries. With our advanced RIM technology, comprehensive tooling expertise, adept process knowledge, and responsive service, we proudly serve as a trusted supplier for both large and small format molding on a global scale.
Are you ready to get started with the reaction injection molding process and enhance your plastic part design?
Our dedicated full-service team is here to support you throughout every phase of your RIM project, from conceptualization and planning to production and fulfillment. Contact us today to request a consultation and explore the benefits of the RIM process.