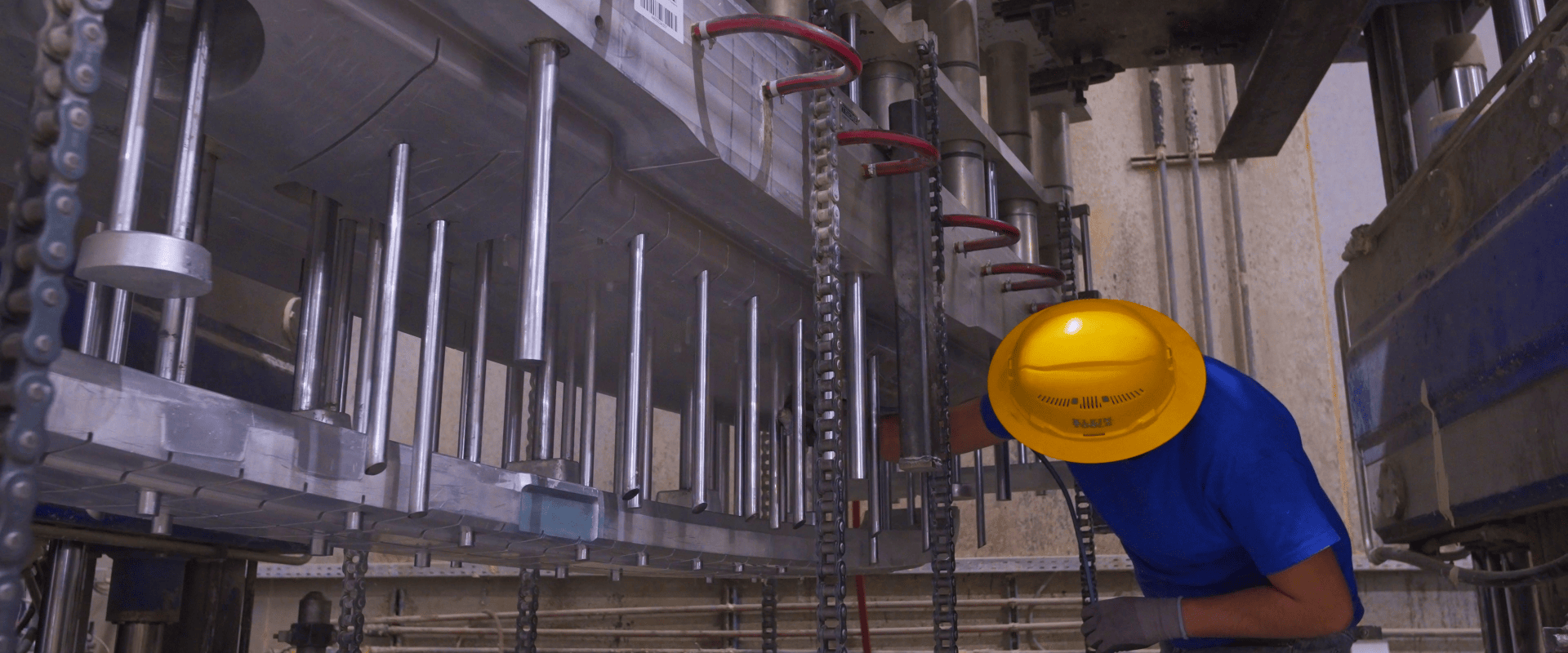
Advantages of Reaction Injection Molding (RIM)
The RIM molding process combines liquid polyurethane resins, low molding pressures, low mold temperatures and provides the ability to mold parts of any size at economical low annual production volumes. It can mimic the physical part characteristics of traditional injection molding, make very large parts like in fiberglass lay-up (FRP), control wall thickness and improve reliability and repeatability of typical labor intensive thermo or pressure formed parts.
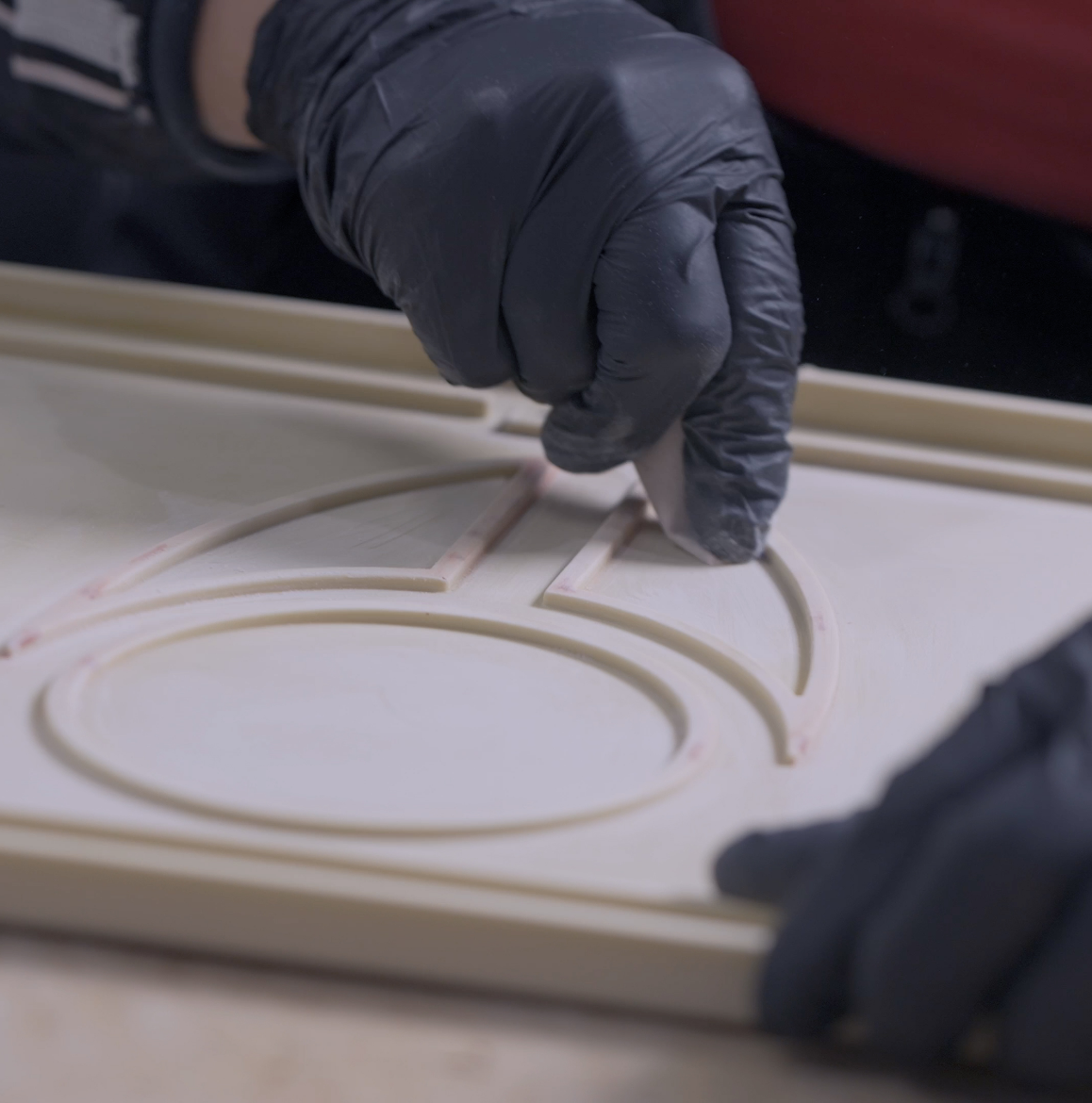
RIM Advantages for a Wide Range of Industries
These RIM advantages can be employed in a host of applications across a diverse section of industries, including but not limited to:
- Medical device
- Laboratory/scientific/analytical device
- Electronics
- Petrol delivery
- Financial/cash handling/POS
- Kiosk
- Casino gaming device
- Heavy equipment/commercial vehicle
- Automotive
- Various other industries
Economic Advantages of Reaction Injection Molding
Low Annual Volume Production Runs
RIM is beneficial for low annual volume production runs as it allows for cost-effective manufacturing of small quantities, avoiding the need for expensive high-volume production processes.
Lower Cost Tooling
Molds used in the RIM process are typically less expensive compared to traditional injection molding, making it a cost-efficient option for producing various parts.
Lower Assembly Costs
The inherent design flexibility of RIM enables the production of complex, integrated parts, reducing the need for extensive post-molding assembly processes and lowering overall assembly costs.
Insert Molding
RIM facilitates insert molding, allowing the incorporation of various materials and components into a single molded part, streamlining the manufacturing process and reducing the need for additional assembly steps.
Repeatability & Reliability
RIM ensures consistent and uniform production of parts, which contributes to lower reject rates and overall production costs.
Cost of Quality
RIM produces dimensionally stable and high-quality parts, reducing the expenses associated with defects, rework, and quality control measures.
Lower Machine Cost
RIM has lower upfront costs compared to some other molding technologies, contributing to overall cost-effectiveness and savings.
Lower Labor Cost to Mold
The efficiency and automation capabilities of RIM processes lead to lower labor costs associated with molding operations, contributing to overall cost savings in the manufacturing process.
Part Design Advantages of Reaction Injection Molding
Large Sized Part Molding
RIM excels in molding large-sized parts, offering a cost-effective solution for manufacturing components that might be challenging or expensive to produce using traditional molding methods.
Deep Draw Capability
RIM’s deep draw capability allows for the production of parts with intricate shapes and deep features, providing flexibility in design and enabling the creation of complex components that meet specific requirements.
Complex Geometry Molding
RIM enables the molding of parts with complex geometries, allowing for intricate designs and detailed features that might be difficult or impossible to achieve with other molding processes.
Molded In Design Features (Sides A & B)
RIM allows the integration of various design features directly into the molded parts, including inserts, slots, venting, holes, bosses, wiring guides, hinges, snap fits, multiple wall thicknesses within the same part, and encapsulation.
Part Consolidation
RIM facilitates part consolidation by combining multiple components into a single molded part, reducing assembly steps, simplifying production processes, and minimizing overall manufacturing costs.
Sheet Metal Conversions
RIM provides an alternative to traditional sheet metal fabrication, offering greater design flexibility, reduced tooling costs, and improved production efficiency.
Excellent Strength to Weight Ratio
RIM parts exhibit an excellent strength-to-weight ratio, providing structural integrity and durability while keeping the overall weight of the part relatively low.
Surface Quality & Impact Resistance
RIM delivers high surface quality and impact resistance, contributing to the overall durability and longevity of the product.
Experience the Advantages of Reaction Injection Molding with Thieme
Thieme provides custom reaction injection molding solutions for a diverse array of devices and industries. Leveraging our RIM technology, extensive tooling expertise, adept process knowledge, and responsive service, we take pride in being a trusted supplier of both large and small format molding to our global clientele.
Are you ready to experience the benefits of reaction injection molding?
Our full-service team is ready to assist you at every stage of your upcoming RIM project, from conceptualization and planning to production and fulfillment. Contact us today to request a consultation and explore the advantages of our RIM services.
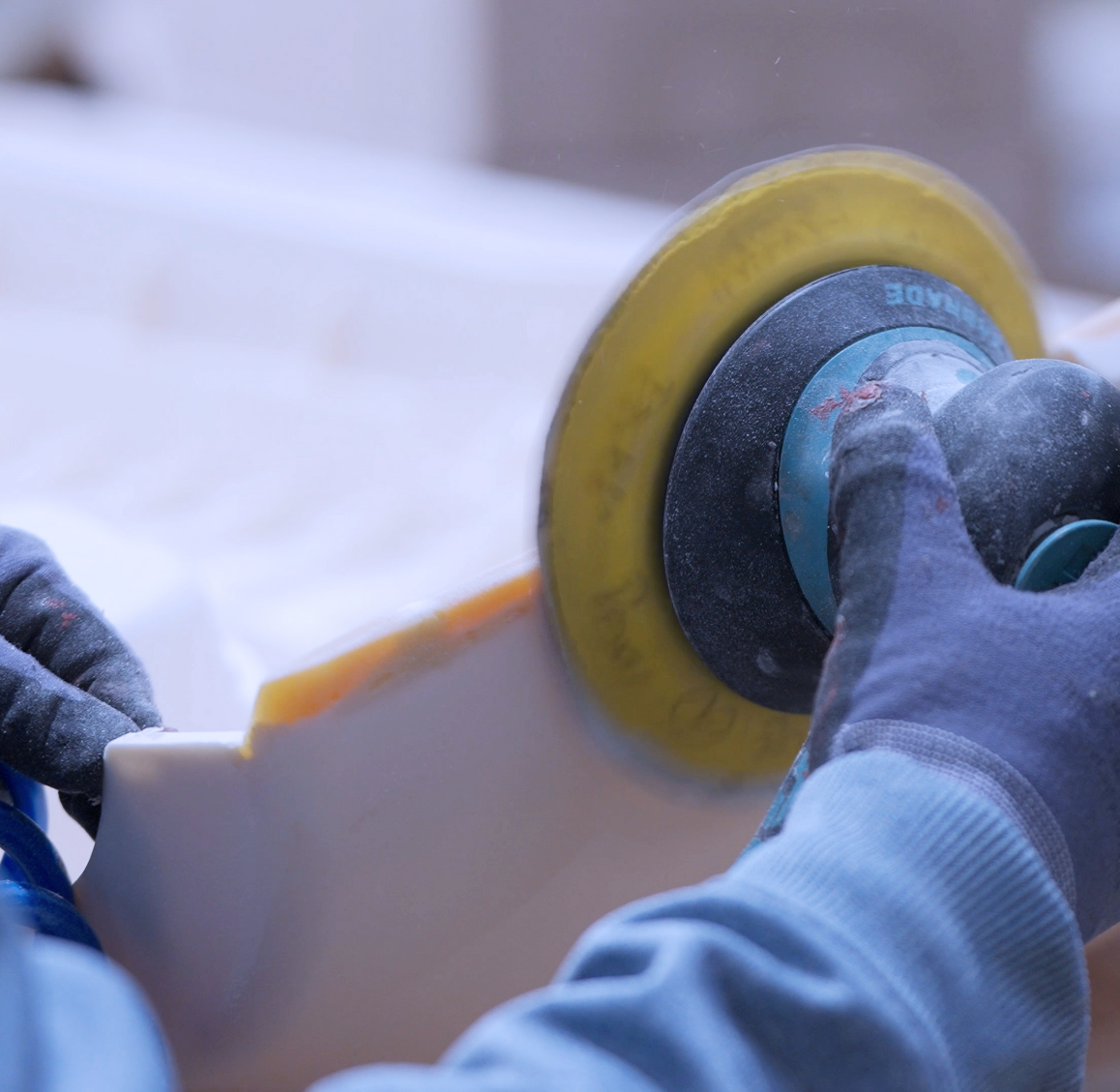