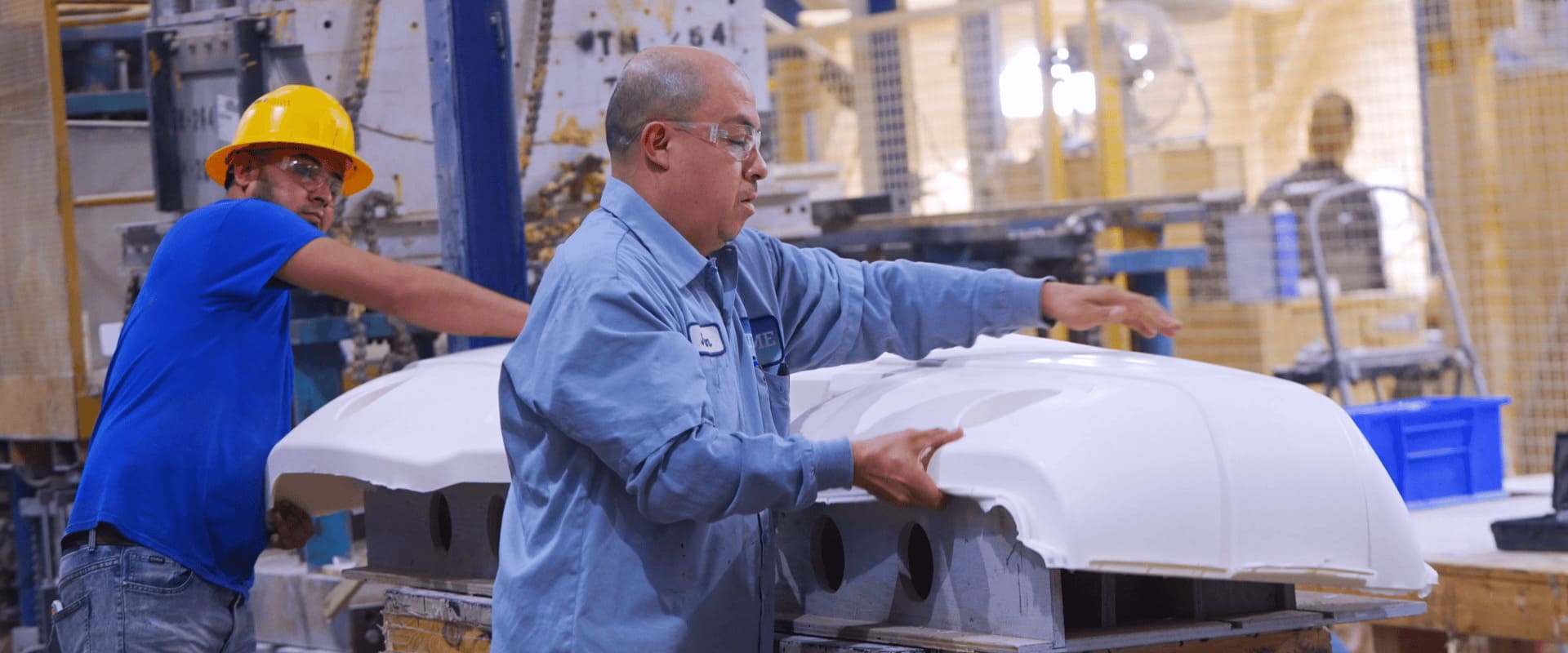
The Industry-Leading RIM Molding Company
Reaction Injection Molding: Low Production Runs
Thieme enables manufacturers to utilize low annual production runs from a few hundred to thousands of parts. When part quality, repeatability, reliability, and low cost are paramount to your project, you can trust Thieme to provide you with the parts and tooling for all stages of your project, from prototype through series production.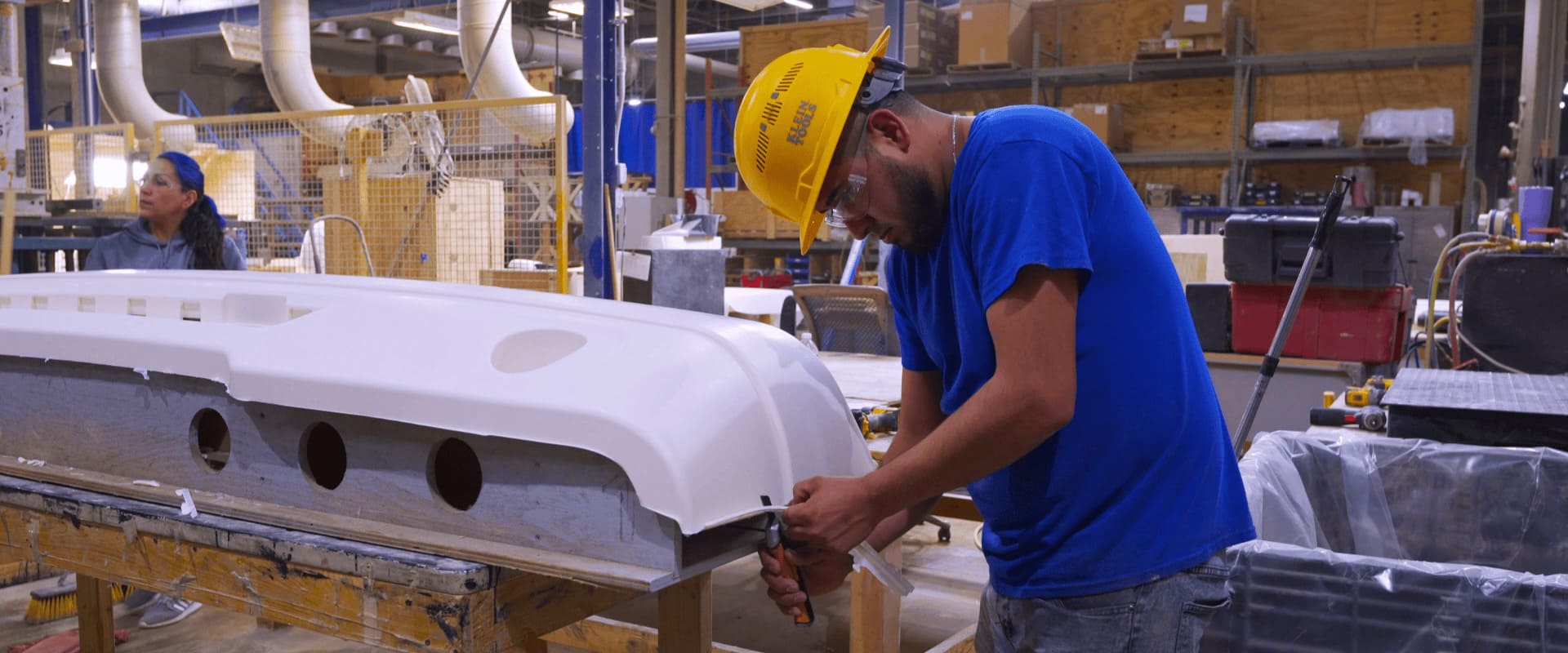
The Industry-Leading RIM Molding Company
Reaction Injection Molding: Functional Design AND Encapsulation
Due to the low temperatures, the inherent adhesion properties of PUR, and the non-destructive liquid temperature of PUR in the mold cavity at injection, RIM and PUR make insert molding and encapsulation of all sorts of materials and objects possible. Inserts, metals, plastics, and other assembly features can be molded into the B-side of the part to help lower your post-mold assembly costs.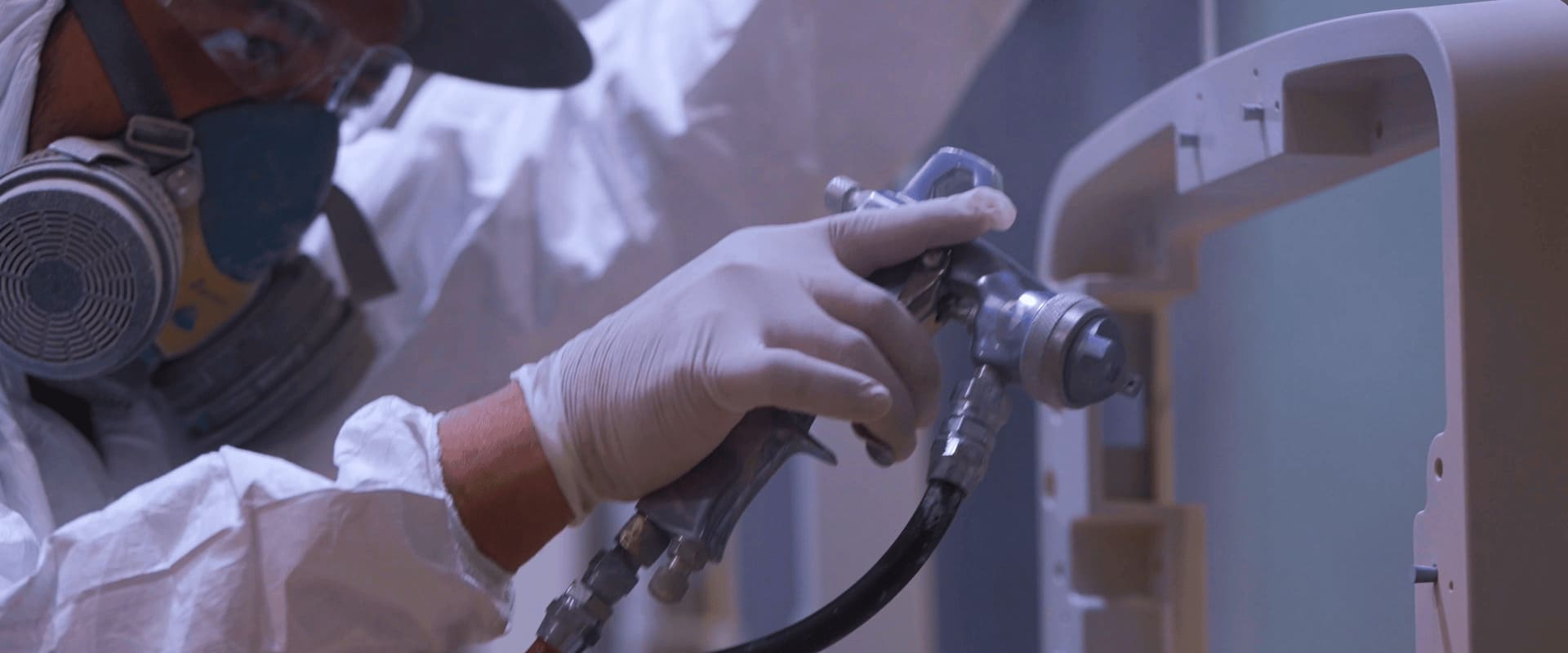
The Industry-Leading RIM Molding Company
Reaction Injection Molding: Creating Parts with Multiple Wall Thicknesses without Sink
RIM allows you to vary your wall thickness from 3mm to 60mm within the same part without sink or distortion. Since the polyurethane material is a thermoset, this sandwich-type foaming system prevents sinks and distortion normally seen in traditional injection molding.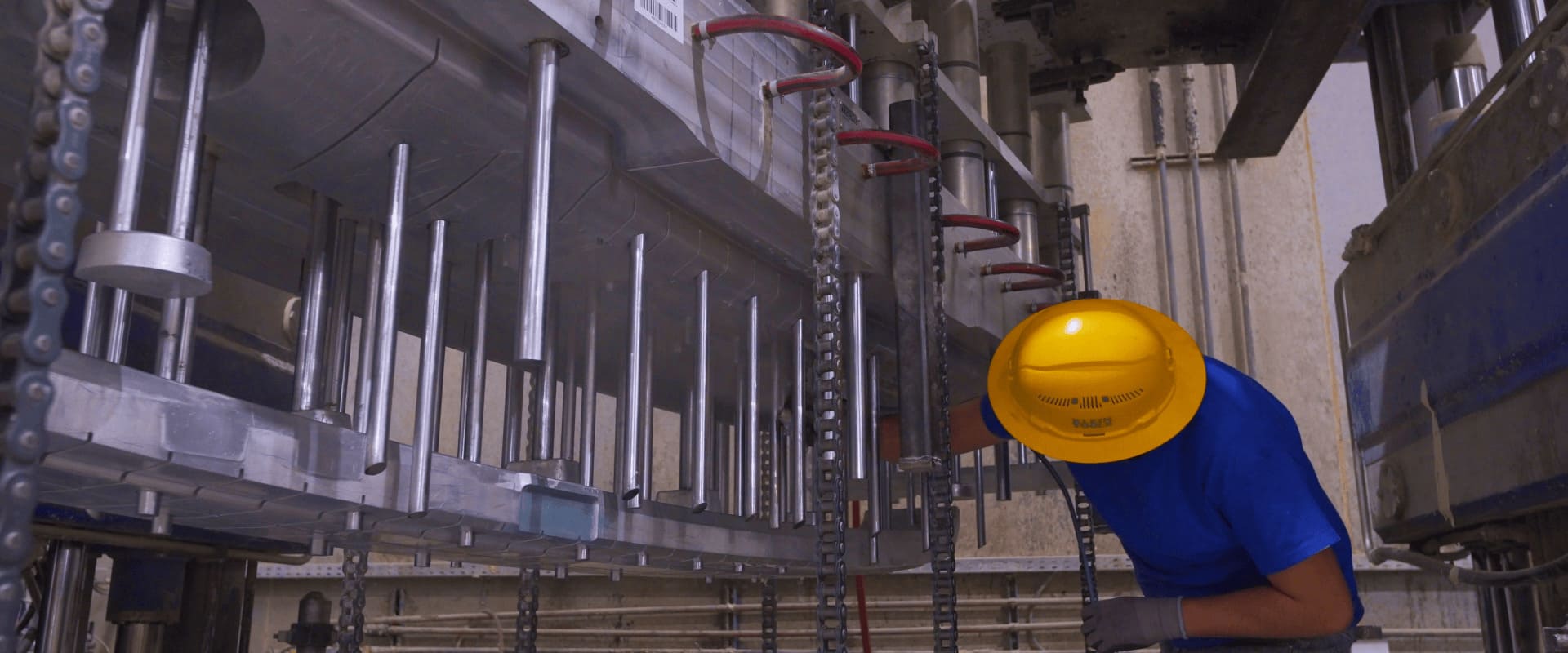
Reaction Injection Molding: Large Part Manufacturing
Since low pressures are used in RIM and considering injection of the gravity fed liquid polyurethane material into the mold, this enables large travel paths within the mold cavity to be possible. Thieme Corporation can mold parts up to 85 pounds in a single shot or with a part footprint of 10' x 8' x 3'.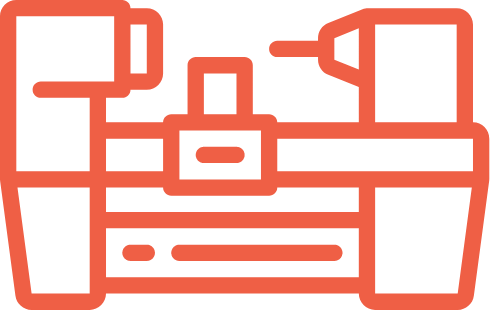
RIM Applications
There are many reasons to utilize RIM molding for your next enclosure, housing, cover, or structural part. We offer low annual volume production (200-20,000 per year), deep draws, large parts, multiple wall sections within the same part, and more...
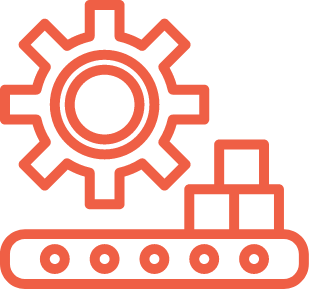
Our RIM Process
Our process is as unique and complete as the parts we make using reaction injection technology. With our 40+ years of experience designing reaction injection parts and tooling, partnering with a top PUR manufacturing company early in your concept/design phase...
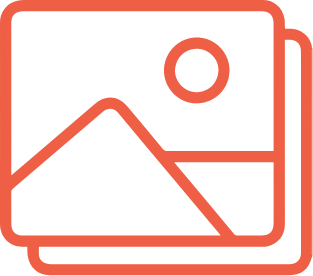
RIM Project Gallery
Have a look inside our project gallery and see the wide array of industries that choose Thieme Corporation and trust our process to achieve success.
What Is Reaction Injection Molding (RIM)?
RIM (reaction injection molding) is a process that involves injecting two liquid raw materials (polyol and isocyanate) separately into a heated mold cavity using only a small amount of pressure. The two liquids combine to create an exothermic reaction where they polymerize to form a molded part.
This RIM process can achieve a broad range of physical properties. Depending on the formulation and mix ratios of the two raw material components of the polyurethane, the finished parts can be foamed, a solid, dual-density foam, and can vary from being flexible to very rigid.

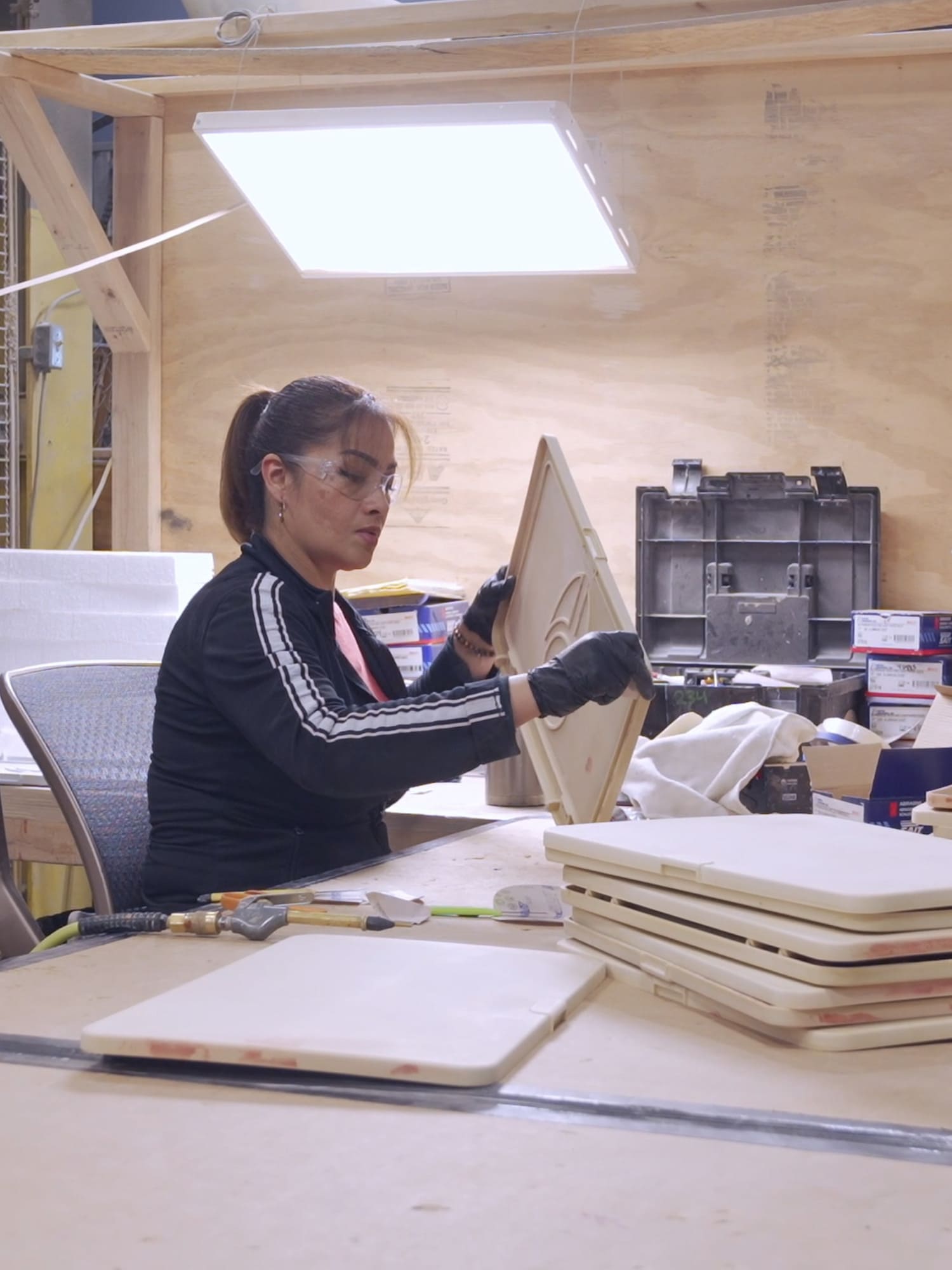
Advantages of Choosing Thieme for Reaction Injection Molding Manufacturing
The RIM molding process holds an array of valuable benefits. Here are a few that our customers have found beneficial:
Cost-Efficient
The reaction injection tooling molding process proves to be more cost-efficient than traditional means of molding, especially at low annual volumes of 5,000 parts or below. This is due to the use of cost-efficient polymer materials.
Versatility
A reaction injection molding company like Thieme knows that reaction injection molding and engineering is an extremely versatile manufacturing process. This method allows for increased creativity since walls of differing thicknesses can be molded in the same part. Parts can be large in size or lightweight. The wall sections can also vary without sink or distortion.
Due to the liquid injection RIM process and nature of the PUR foaming process, unique, difficult, deep-drawn, and cylindrical parts can be achieved.
A Full-Service Reaction Injection Molding Company
Additional RIM Services
- Product Design Assistance
- Medical Device
- Feasibility Studies
- Tool Design & Manufacturing
- Simulation & FEA Analysis
- Prototype Development & Delivery
- Production Molding Services
- Painting & Surface Coatings
- EMI Shielding, HLA Services
- Value Added Assembly & Kitting
- Logistics & Packaging
- Product Fulfillment & Complete Project & Program Management
Request a Proposal for Your RIM Project Today!
Thieme offers affordable reaction injection molding tooling solutions for companies everywhere. Request a Proposal Now!