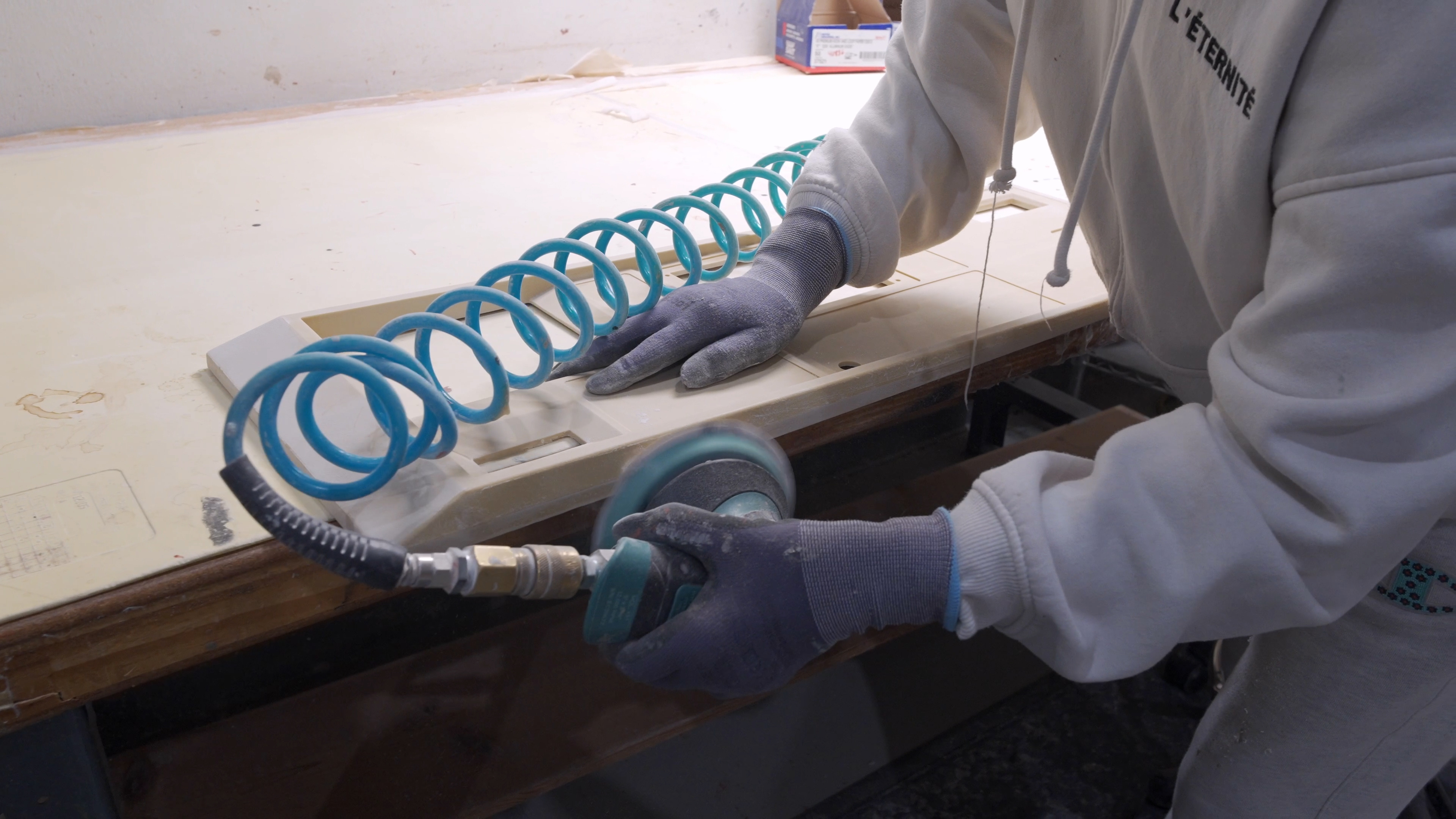
RIM Tooling Design and Manufacturing
Unlike traditional injection molding, RIM tooling uses lower cost aluminum tools to mold parts from. Since the physical performance characteristics of the polyurethane material systems require constant surface temperature and control in the mold, aluminum provides a cost effective way to achieve that.
The tools can be cast or CNC cut using aluminum billets. Tool actions such as sliders, hydraulics, lifters, fists and inserts can be engineered into the RIM tool. Each RIM tool is built to the exacting Thieme Tool standards. Gating location, material shrink, venting and other mold construction standards are all included. At Thieme Corporation all RIM tools are designed by Thieme tool engineers.
Thieme Corporation designs all of its RIM molding tools and only uses NC Cut aluminum tool and Thieme selected components to ensure correct material system performance characteristics as recommended by the raw material suppliers.
All tooling manufactured by Thieme Corporation will produce parts for the series life of the project.
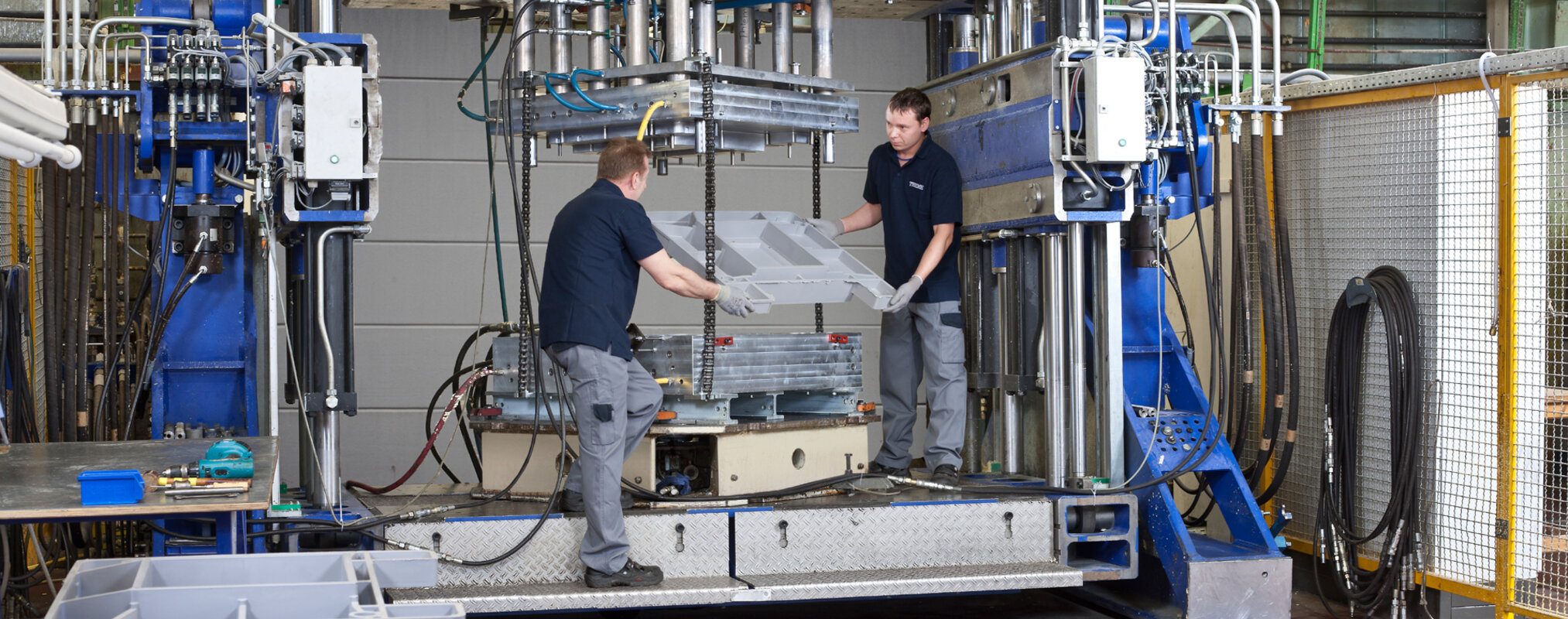
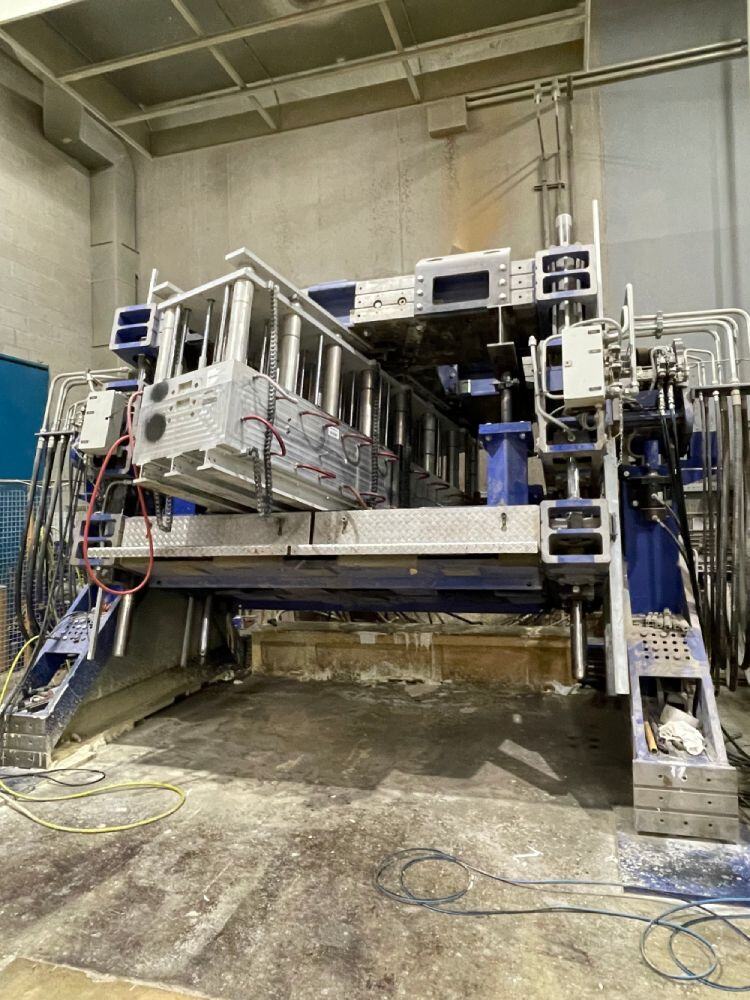
Shrinkage
- All shrinkage for the material systems are built into the tooling.
Dimensional Tolerances
- These tolerances are based on a number of variables including, part density, mold temperature, mold alignment, injection rate, demolding time, component ratios, temperature, mold pressure and other production conditions.
- All Thieme Corporation molding systems are close-loop systems which monitor all processing parameters to ensure quality.
Edge Gating
- Always gate at the edge of the mold
- Locate at the lowest point of the mold
- Locate on a straight parting line section
- Locate based on the lowest flow length of the material through the mold
- Locate the gate on a less noticeable area or a non aesthetic area of the part
- Locate the gate so the flow is parallel to designed in ribs
Mold Venting
- Have vent locations at the highest point in the mold cavity
- Maximize vents to assist in filling
- Make vents wide and shallow not narrow and deep
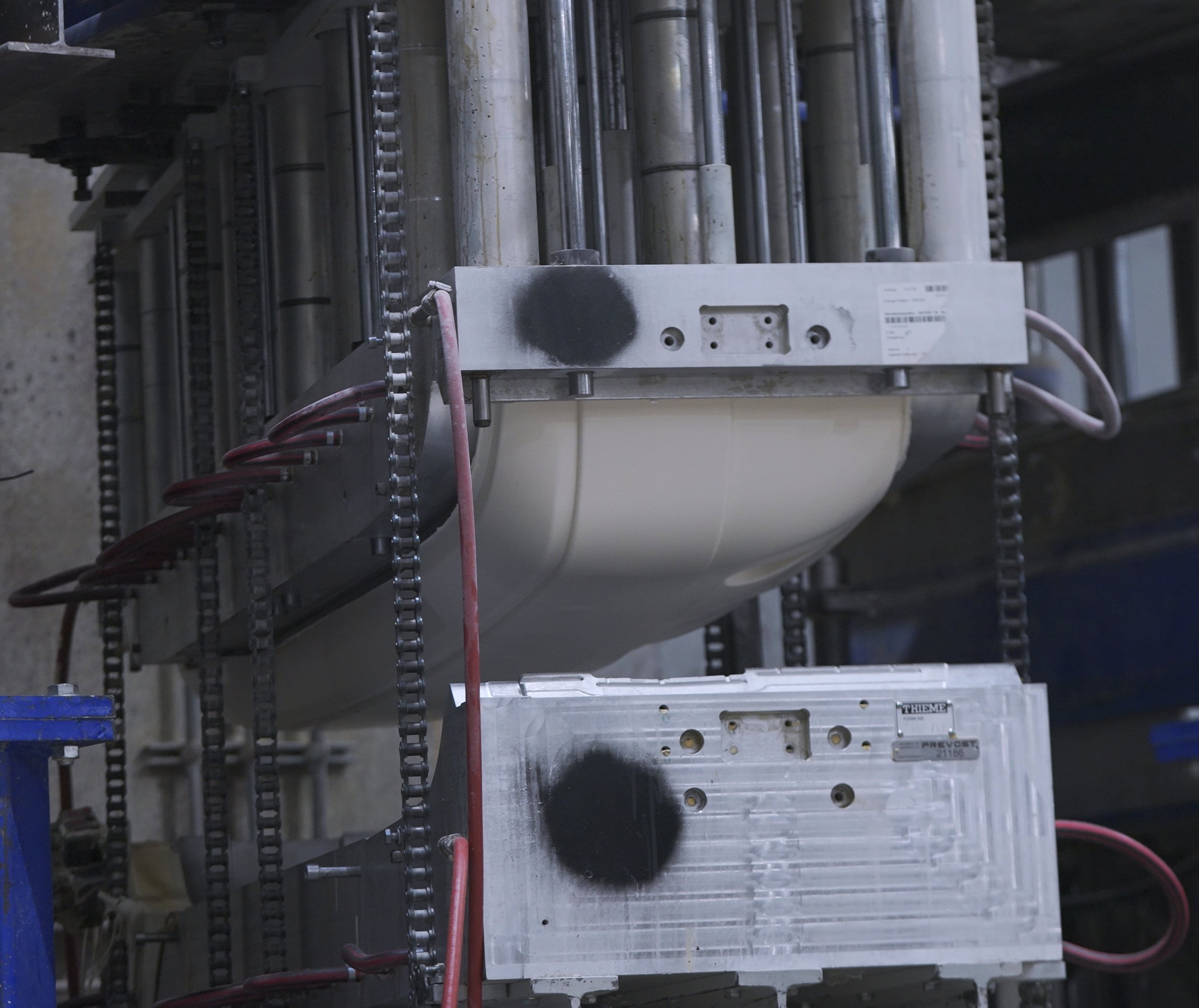