Converting Thermoformed Pieces into Robust Parts Using the RIM Process
Across industries and manufacturing, plastic materials are used to build pieces that can then be assembled into larger, more complex products. The reaction injection molding (RIM) process is one of many manufacturing methods used to design and mold plastic parts and comes with several advantages compared to other methods, such as thermoforming.
If you want to develop robust, reliable, single-piece plastic parts, consider RIM.
Thermoforming vs. RIM
Thermoforming is the process of heating a sheet of plastic until it is pliable and then shaping the sheet against a mold using a vacuum or air pressure until it reaches the desired shape. Through this method, you can achieve variable wall thicknesses, details, textures, and volumes of parts.
RIM involves injecting a mixture of two liquid materials (polyol and isocyanate) into a mold to form a polyurethane polymer part. With RIM, you can create pieces with significant wall thickness variations and extremely intricate parts, all in one piece if needed.
While thermoforming is ideal for many simple geometry designed parts, There are many post mold operations to perform such as ribbing, structural supports, boss blocks and numerous gluing operations on the B-side of the thermoformed part. RIM is the best option for products that require complexity on the B-side of the part , deep draw features and consistent quality for their location and accuracy of the molded in features on the B-side of the part.
An Example of Redesigning Thermoformed Parts with RIM
By converting the design of plastic components from the thermoformed process to the RIM process, you can develop more robust products, among other benefits of RIM.
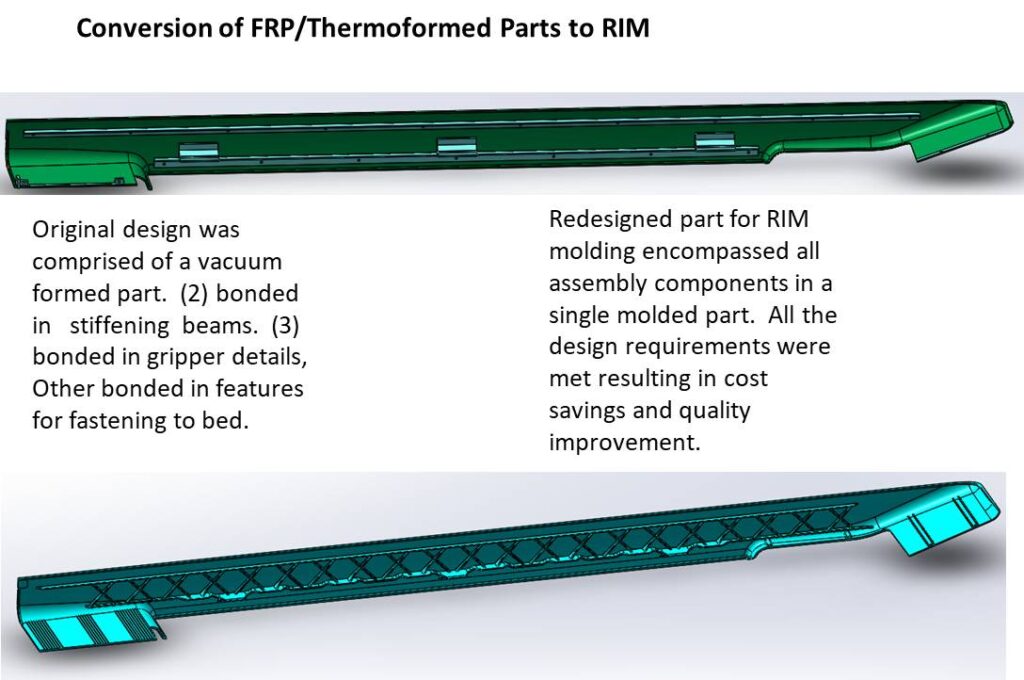
In the original thermoformed design (Figure 1), the piece consisted of several vacuumed-formed parts: two bonded stiffening beams, two bonded fastening blocks, one bonded spacer/stop plate, two guide tabs, and one O-ring retaining strip. Additionally, the process itself does not allow for the control of your wall sections as you are stretching material over your desired features of size. These post mold operations drive up assembly/part costs and also subjects the part to possible quality issues in controlling location accuracy, features of size and repeatability.
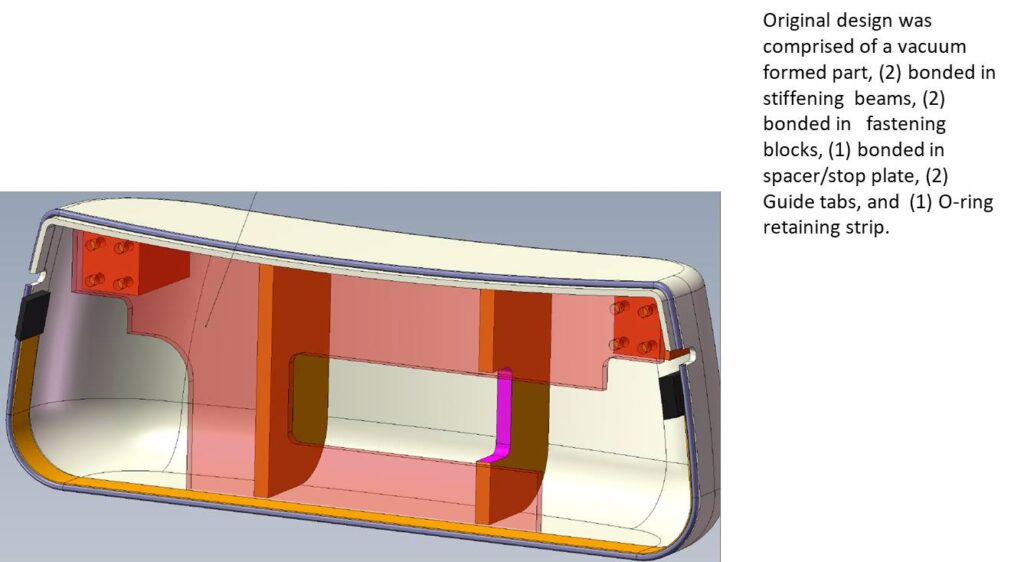
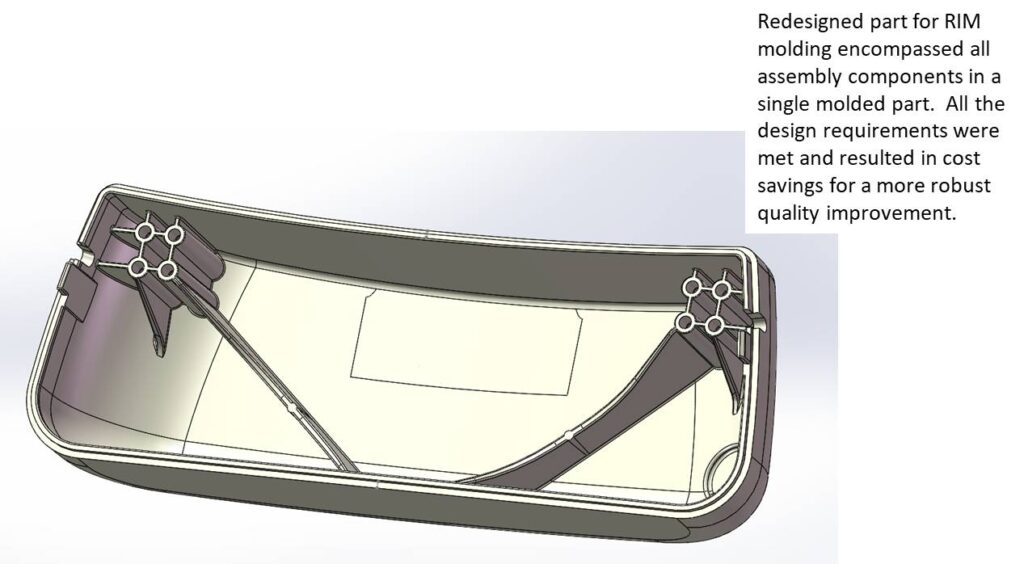
Through the RIM process, the piece can be redesigned as a single molded part that includes all assembly components molded in. The result is a high-quality, robust product that controls the location, accuracy and the feature of size. In the end the part cost will be lower and your quality will be increased over a thermoformed part. as well as significant cost savings.
Contact Thieme to Get Started with Reaction Injection Molding
At Thieme, we offer custom reaction injection molding for a wide range of devices and industries. With our RIM technology, tooling knowledge, process expertise, responsive service, and exceptional approach to project management, we are proud to serve as a trusted supplier of large format (and small) molding for our global customer base.
We specialize in customized RIM projects in a variety of industries and applications, including device enclosures, structural parts, analytical instrumentation, medical device parts, and various industrial devices and machinery. Additionally, you can explore our options for large format molding for heavy equipment, automotive, medical, and other industries.
Are you ready to upgrade your approach to designing plastic parts using reaction injection molding?
Our experienced full-service team is ready to help you with every part of your next RIM project, from conception and planning to production and fulfillment. Contact us today to request a consultation and discover how you can benefit from our RIM services.
Post a comment